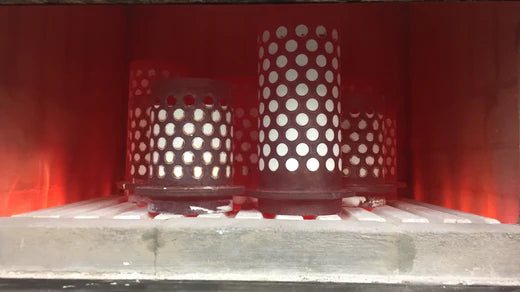
Casting and Burnout Cycle for PowerResins Castable Resins
Share
A Guide to Post-Processing and Ash-Free Burnout Jewelry Casting Cycle
In this guide, we share our recommended burnout cycle, used by one of the industry’s top casting houses, while noting that many of our customers find success with slightly varied processes as casting cycle having many inputs which effect directly to the results. We’ll walk you through each step, from post-print washing to the burnout cycle, so you can achieve the best casting for your jewelry designs.
Start with the Basics: Follow Your Investment Brand’s Specifications
Make sure you are using an investment brand which is specifically produced for resin casting. These important steps typically include:
- Water-to-Powder Ratio: Use a precise scale for accurate measurement. Use distilled water for the best performance.
- Mixing Process and Time: Invest in proper equipment to ensure consistent results.
- Flask Resting Time: Follow the recommended time before inserting the flask into the oven. Typically wait at least 3 hours.
- Burnout Cycle: The optimal schedule for resin removal.
- Casting and Pressure Control: Fine-tuning your machine settings for best results.
These elements play a pivotal role in casting quality, along with factors such as the cylinder size, oven efficiency, and even the washing technique used after printing.
Step 1: Washing the Models Properly
A clean model is essential for a high-quality casting. Here’s our recommended washing method:
- Alcohol Choice: Ethyl alcohol is recommended, but isopropyl alcohol can also work.
1.Initial Clean: Rinse your model for 3 minutes in an alcohol alcohol (at least 96% pure ethanol or IPA) basket or in ultrasonic cleaner.
2.Second Wash: Submerge the model for 2 minutes in cleaner second alcohol basket. Afterward, dry with compressed air.
3.Final Rinse: Dip again for 2 minutes in fresh alcohol, then dry thoroughly.
4.Inspection: Check for any remaining uncured resin. If you find any, repeat the cleaning steps as necessary.
- Timing: Limit total alcohol exposure to 6 minutes to prevent damage or negative effect to casting.
Storage: To maintain model integrity, cast within 2 hours of cleaning. If immediate casting isn’t possible, store the models in a dark, sealed plastic bag without washing.
Pro Tip: Using compressed air for drying ensures thorough cleaning and speeds up the process, which can help prevent casting flaws.
Step 2: Mastering the Investment Process
The investment stage is just as critical. Here’s what you need to know:
- Follow Manufacturer Instructions: This includes the water-to-powder ratio, mixing duration, and setting times. Correct measurements and timing lead to optimal results.
- Ensure Proper Vacuuming: Invest in professional vacuum equipment to remove air bubbles and create a strong investment. Vibrating the investment during vacuuming enhances results.
- Optimal Tree Placement: Position the casting tree far from the flask’s edge, as this prevents expansion issues and allows metal to flow smoothly during casting.
Note: Each of these steps requires professional-grade equipment. Paying attention to detail at this stage can make all the difference in casting quality.
3. Recommended Burnout Cycle
The burnout cycle is the final preparation before casting. Here’s the ideal schedule:
- Let the Flask Settle: Before inserting it into the furnace, let the flask rest for at least 3 hours.
-
Temperature Control:
- Final Stage: Gradually ramp down to 600°C over an hour. Then, maintain the flask at 600°C for another hour before pouring the metal.
- Use Fresh Metal: Avoid casting with metal that has been used more than 3-4 times, as repeated use can degrade casting quality.
This cycle helps ensure that the resin burns out completely, leaving no residue behind and creating a clean mold for metal pouring.
Need Assistance? We’re Here to Help!
At 3BFAB with our brands PowerResins, NovaFab and DentaFab, we’re committed to helping you achieve casting excellence. If you have questions or need personalized guidance, feel free to reach out to us at support@3bfab.com. We also invite you to join our Facebook user group here to connect with other PowerResins castable resin users, exchange tips, and gain insights on best practices.